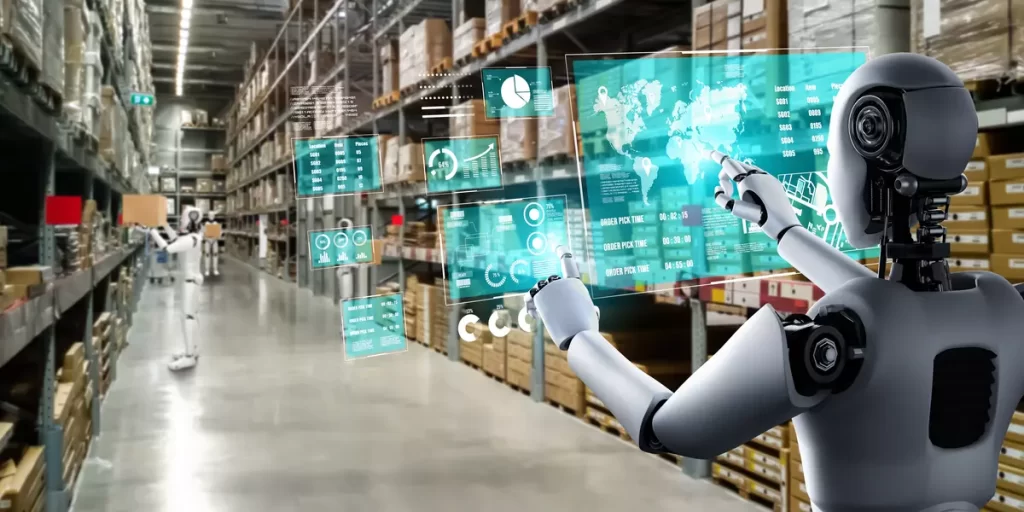
The automotive industry constantly strives to find new ways to improve efficiency and productivity while ensuring they remain competitive. One of the solutions that businesses have begun implementing is using collaborative robots in their manufacturing and subcontracting processes.
With improved accuracy, speed, and cost-effectiveness compared to manual labor or traditional automation solutions, it’s no wonder these versatile robotic technologies are appearing more frequently in production lines worldwide. In this article, we’ll explore how robotics technology has been changing how automotive companies do business – from significant OEMs to local component manufacturers.
Understanding the Benefits of Collaborative Robots in Automotive and Subcontracting Industries
Collaborative robots have been proving very beneficial in automotive and subcontracting industries recently. Otherwise known as cobots, they have been immensely helpful in improving the efficiency and accuracy of manufacturing processes in these industries. Cobots are increasingly becoming a preferred choice in the production line due to their ability to work alongside humans without compromising safety.
They allow for increased flexibility in production schedules and can easily be programmed to carry out a wide range of complex tasks. Cobots have also been instrumental in reducing production costs and allowing more time to be allocated to quality inspection. With these benefits in mind, it is no surprise that the use of cobots in manufacturing robots is rising in these two industries.
Exploring Automation and Its Many Uses
Automation has been integral to the automotive industry for many years, and its applications are becoming increasingly varied. It is now used for improved efficiency in materials handling, assembly, welding, painting, etc. Automation systems allow companies to move quickly and accurately between processes more consistently than manual labor could achieve. In addition, automation can be highly cost-effective compared to traditional manufacturing methods.
It can also improve safety by reducing the risk of human error in complex operations like welding or painting. Automation technology is even used in supply chain management to enable better communication between OEMs and subcontractors for improved speed and accuracy throughout production.
Identifying Challenges Faced by Automotive and Subcontractors
Despite the many benefits of automation, there are still a few challenges that automotive and subcontracting companies must face. One of these is cost – automation systems can be expensive to deploy and maintain, which can be prohibitive for small-scale businesses. Additionally, setting up these systems requires expert programming and robotics engineering knowledge, which can add further costs.
Another challenge is safety – if not implemented correctly, automation systems can pose risks to employees during operation or even when they’re being maintained. Finally, there is the issue of integration with existing manufacturing processes which requires careful planning and consideration before implementation.
Assessing the Impact of Robotics on Workforce Dynamics
The introduction of robotics technology has had a significant impact on the way automotive and subcontracting businesses operate. As automation becomes more pervasive, human labor is being replaced by machines in many areas of production which has caused some disruption to the workforce. On the other hand, it has also been beneficial as it frees employees from mundane, repetitive tasks and allows them to focus on higher-value activities requiring creative thinking or problem-solving skills.
In addition, automation can help reduce costs associated with wages, training, and insurance while increasing productivity and accuracy in manufacturing processes. It means that companies can get more out of their resources while giving employees a better quality of work life. The impact of robotics on workforce dynamics should be carefully considered when introducing automation into the production line.
Examining the Benefits of Collaborative Robots for Automotive and Subcontractors
Collaborative robots have become an increasingly popular choice for automotive and subcontracting companies due to their cost-effectiveness, speed, and accuracy compared to traditional automation solutions. They are also simple to deploy and maintain, with little programming or robotics engineering expertise.
These versatile robots can be programmed to carry out a wide range of tasks from materials handling to assembly and welding – all without compromising safety. The use of cobots has enabled improved efficiency across the entire production process as well as saved time on quality control. It is why they are becoming an essential tool in the manufacturing lines of leading automotive companies worldwide.
How to Implement Collaborative Robotics into Automotive and Subcontractor Business Practices
If your automotive or subcontracting business is looking to implement collaborative robotics into its production process, a few key considerations need to be made. Firstly, you must determine the tasks that can be automated and carefully plan out how the robots will fit into the existing workflow. It involves understanding the capabilities of each robot and how it should interact with other systems to maximize efficiency.
Before deploying any robotics technology in your facility, you should ensure that all safety risks have been considered. Finally, you must ensure adequate training is provided to staff so they know how to use and maintain the robots correctly.